Fabricated steel is usually primed in the shop and at times requires welding in the field. Most alkyd (oil) based primers will burn away immediately and turn to dust. This leaves the weld and weld area without any corrosion protection. Often, it will begin rusting within days. There are a number of factors that cause weld material to rust. For a better understanding of what causes Weldment Corrosion ASM offers an in-depth review “Basic Understanding of Weld Corrosion.” (click)
The exposed weld can be re-coated but often this difficult to do in the field. The Steel Supply Company offers two possible alternatives; Weldable Primer and Aerosol Primer.
Weldable Primer;
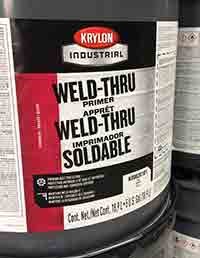
Very similar to a basic shop coat Weldable Primer is applied in the fabricating shop by spray or roller. It will coat and protect the steel and even look the same as regular shop coat. However it has an added feature. Zinc is infused into the mixture, not as a protectant like the zinc used in Hot Dip Galvanizing, but to react with the weld material. The zinc resides in the primer coat after curing. As the active weld process reaches approximately 3,000°F /1,650°C the zinc in the primer melts and infuses with the weld material. Once cooled the weld material now has the zinc acting as corrosion resistance. This affords some protection against rust. How effective it is depends on the weld, weld material, penetration, moisture, etc.
Aerosol Primer;
A good method to re-coat welds when the shop coat primer has burned away is Steel Supply’s Aerosol Primer. Available in Red Oxide or Gray in 16oz. cans are easy to transport and use at the jobsite. These are specially designed coatings with strong resins that will aid in corrosion resistance. One or two coats can be applied depending on the protection desired. Aerosol primers have the advantage of drying to the touch in 15 minutes and can be recoated at any time. Like any coating it serves much better protection if the substrate is clean and free of contaminants. After welding through primer there will residual dust and any other debris collected during installation. A wire brush is a good way to clear the substrate and assure maximum performance of the coating.
Cold Galvanize Compounds are excellent rust preventative coatings but are not designed to be coated over. For this reason one method that should not be attempted is to coat the exposed area with Cold Galvanize, then spray or brush a primer coat over that. By its nature, oil based coatings will not adhere to zinc coatings whether the zinc is Hot Dip or Cold Galvanize applied. The zinc present in either of these coatings will chemically react with the binders of any oil based paint. This reaction causes saponification (a soapy film layer) on the galvanized surface. While initially the primer coat will appear to adhere, as this chemical reaction develops the top layer of paint will soon peel off.