When manufacturing made to order steel wedges there are a number of ways it can be done and usually the configuration dictates what method is selected. Some of these are outlined in a previous blog, Steel Wedge Manufacturing. The Steel Wedge we are focusing on in this conversation is required as part of a Fluorogold® or Teflon® Slide Bearing Assembly. Length is 20", Width is 14". Thickness starts at 1/2" and tapers down to 1/16". The unique size of this wedge dictates the manufacturing process.
Often wedge dimensions allow for "splitting" a block to produce two blanks which are then machined to the finished size.
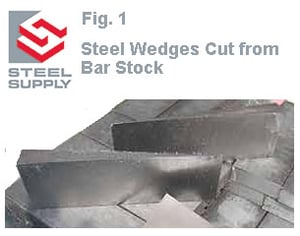
Figure 1 shows an example of splitting bar stock to form two wedges. The dimensions are 12" long x 4" wide. The thickness tapers from 1" down to 1/8". Starting with Flat Bar stock 1-1/4" x 4" the blocks are cut 12" long. Each block is cut diagonally to produce two wedges. The edges are 1" + approximately 3/32" removed by the kerf of the saw blade + the 1/8" required for the narrow end of the opposite wedge. Often, in projects such as concrete shoring or underpinning this is more than accurate enough to be used as is. In permanent structural applications machining is required to bring the wedge within tolerance and produce a smooth and more finished appearance.
In cases like these Stock Wedge sizes often fill the requirements. Click here for a list of Steel Wedges in stock.
Figure 2 shows a wedge whose dimensions and intended use dictates an entirely different manufacturing process.
Wedges of this size and length cannot be made as split wedges. Initially, very few shops have a band-saw capable of a 20" long cut, 14" deep. Further, it is impossible to hold the material in place during the cut and even if that problem was solved the band-saw blade would deflect out the side of the narrow edge.
Additionally the function in this case requires the wedge surface be more accurate and smooth. As mentioned above this wedge will act as a substrate on a Slide Bearing Assembly. The correct angle is essential as well as a uniform surface to evenly disperse the bearing load. For this wedge we start with 1/2" thick plate steel, cut to 20" x 14" and machine the taper using a vertical milling machine. The taper is done in broad strokes, side to side. Stress relief will cause this wedge to tend to curve inward. As well, heat created by the milling process can exacerbate the warping. For this reason the milling is done in small increments and advance at a low rate of speed.